Worldwide Installations are a testament to the service, partnership and unique understanding we can apply to create unique solutions dedicated to the demands and mix of individual businesses and regions. From full scale plant design, to individual mixing, dispersion and in-line filling an opportunity exists to improve any business.
Comec primary area of experience is in working with and providing solutions to businesses operating in the Coatings and Inks, Adhesives and Sealants, Chemical, Food and Cosmetic sectors.
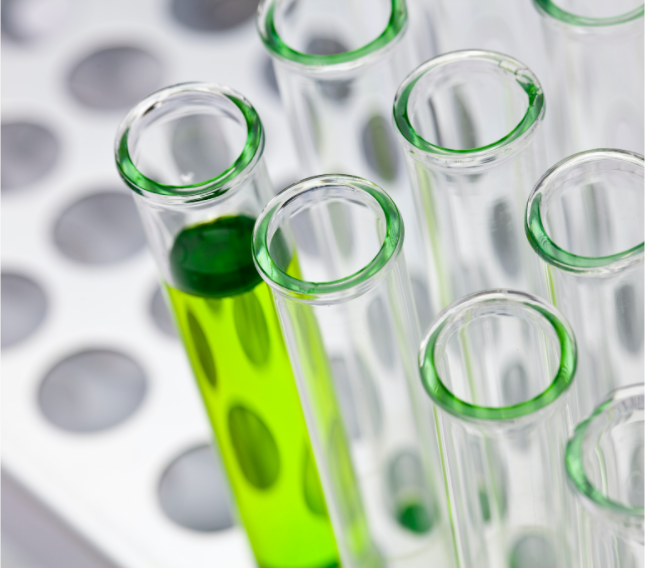
Adhesives and Sealants
Raw materials can have significant cost impacts and waste control and cleaning can create significant complexities that need to be minimized and resolved within the Production Process. We have developed a wide range of solutions through the Value Chain, from rationalizing storage and distribution of chemical components to the closed processes of dosing, blending and mixing. Finally, to high-speed precise filling, packaging and palletization, optimal customized solutions are created. The benefits of this are stable, lean systems with a high level of repeatability in a safe and automated environment.
Food and Flavours
The food industry has seen many of the most dynamic and diverse changes in Value Chain and Production Processes over the last twenty years. At the same time meeting the diverse and highly regulated levels of international health and safety requirements has added further complexities and costs in a category where margins can be small and micro cost control critical. The speed of dispersion of solids into liquids, the raw material utilization from closed loop systems and the plant utilization of a 24/7 operation all require the highest levels of equipment, monitoring and design.
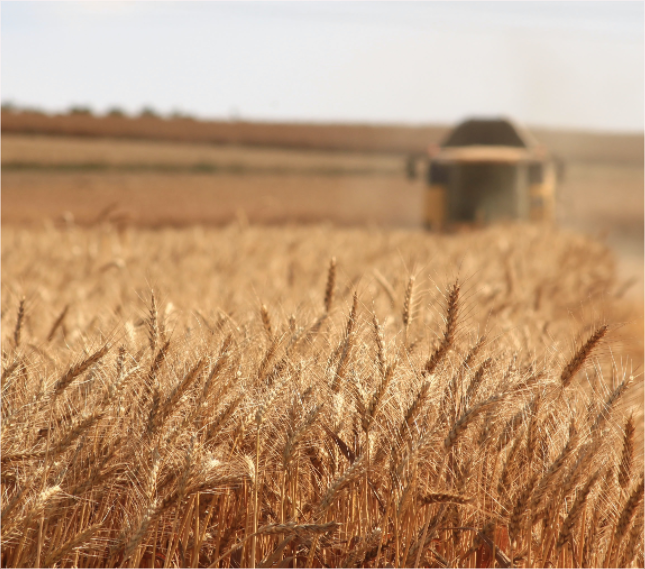
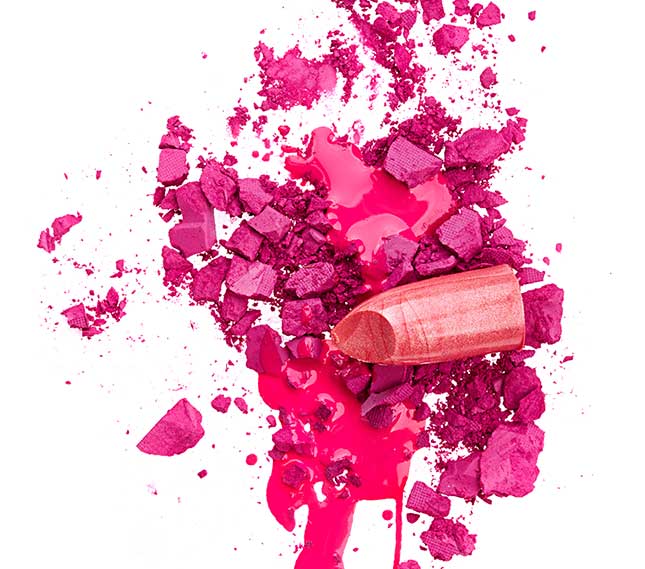
Cosmetics and Emulsions
Dedicated equipment is suitable for many applications for a stable dispersion of oils into water, for adding pigments and glues and for mixing colorant into products including small batch products like nail lacquers. The development of Micronet technology has created the ability to disperse and mill at the same time, leading to a reduction of the cycle and halving cleaning operations. The significant benefit can be measured in a reduction of downtime and increases in productivity.
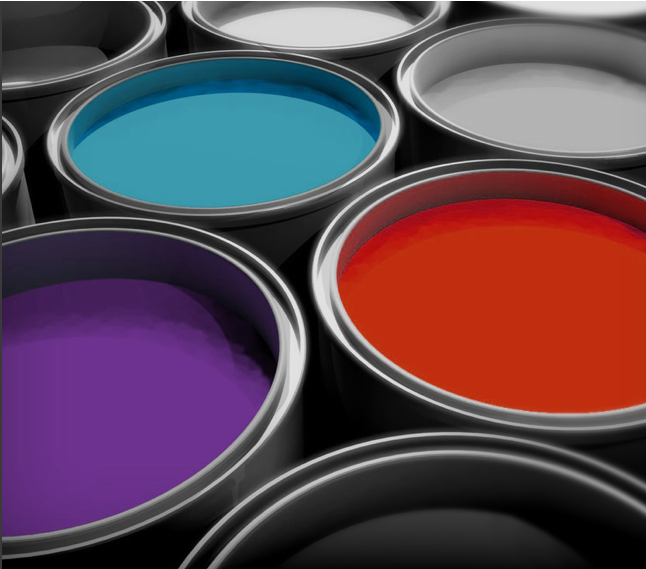
Coatings and Inks
Worldwide Installations are a testament to the service, partnership and unique understanding we can apply to create unique solutions dedicated to the demands and mix of individual businesses and regions. From full scale plant design, to individual mixing, dispersion and in-line filling an opportunity exists to improve any business.
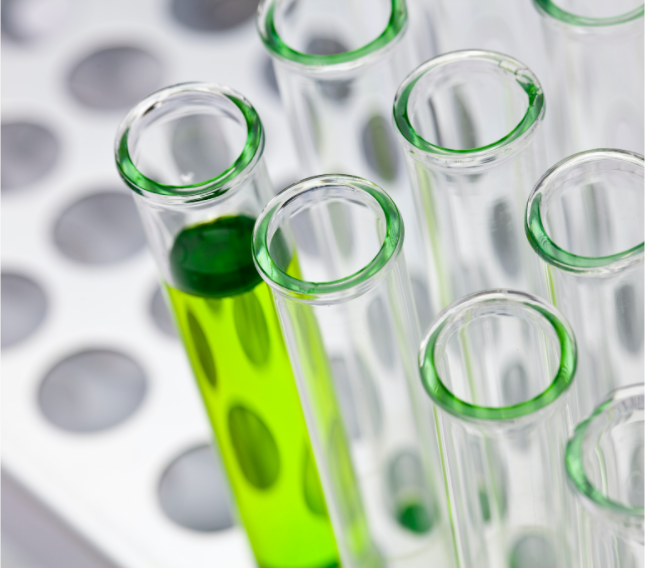
Adhesives and Sealants
Raw materials can have significant cost impacts and waste control and cleaning can create significant complexities that need to be minimized and resolved within the Production Process. We have developed a wide range of solutions through the Value Chain, from rationalizing storage and distribution of chemical components to the closed processes of dosing, blending and mixing. Finally, to high-speed precise filling, packaging and palletization, optimal customized solutions are created. The benefits of this are stable, lean systems with a high level of repeatability in a safe and automated environment.
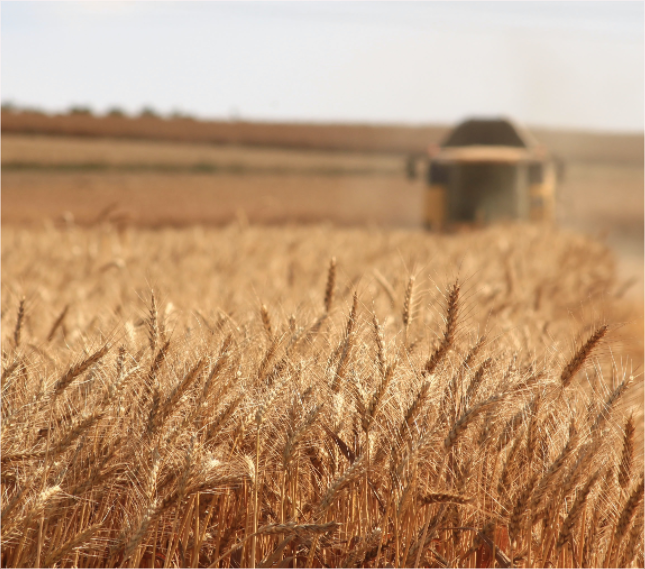
Food and Flavours
The food industry has seen many of the most dynamic and diverse changes in Value Chain and Production Processes over the last twenty years. At the same time meeting the diverse and highly regulated levels of international health and safety requirements has added further complexities and costs in a category where margins can be small and micro cost control critical. The speed of dispersion of solids into liquids, the raw material utilization from closed loop systems and the plant utilization of a 24/7 operation all require the highest levels of equipment, monitoring and design.
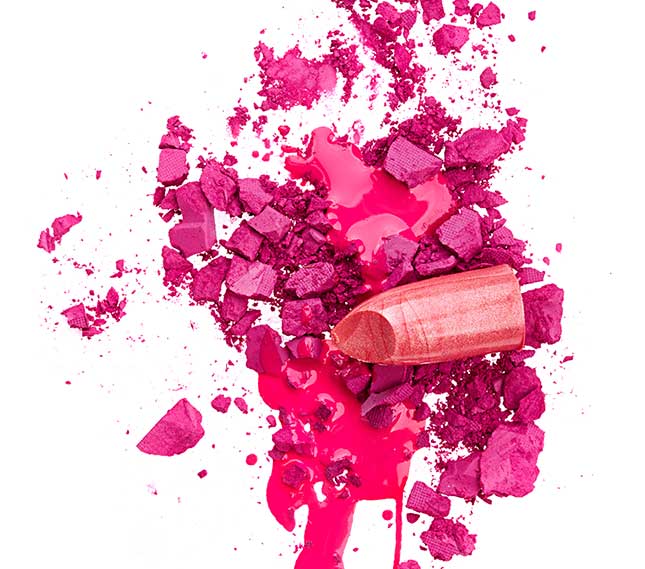
Cosmetics and Emulsions
Dedicated equipment is suitable for many applications for a stable dispersion of oils into water, for adding pigments and glues and for mixing colorant into products including small batch products like nail lacquers. The development of Micronet technology has created the ability to disperse and mill at the same time, leading to a reduction of the cycle and halving cleaning operations. The significant benefit can be measured in a reduction of downtime and increases in productivity.